
There are two primary types of subtractive chemical processes: (non-spontaneous) electrochemical processes and purely chemical processes. In reality, both processes are (on a very technical level) electrochemical processes as they involve the transfer of electrons, but for simplicity, we will refer to spontaneous (galvanic/voltaic) processes as purely chemical and non-spontaneous electrochemical/electrolytic processes as electrochemical in this article. Both types of processes have advantages and disadvantages when used as subtractive, material removal operations. There are, of course, many electrochemical (ex. electroplating) and purely chemical processes (ex. passivation) that do not have a primary purpose of removing metal from a component, but these processes will not be covered in this column.
Purely chemical processes
Purely chemical processes (or more specifically spontaneous galvanic electrochemical processes where ΔG0 < 0 and ΔG is the Gibbs free energy of the reaction) that subtractively remove metal from a component are commonly referred to as chemical milling or chemical etching. Less frequently, these processes may be referred to as chemical polishing. In fact, these terms refer to three different processes, although there can be strong similarities between them.
Chemical milling (CM) is perhaps best described as the controlled dissolution of the surface material from a component. CM is, generally speaking, a bulk material process, and can be referred to as chemical machining.
Chemical etching (CE) could be considered a derivative process from CM in that it also is a controlled chemical dissolution of surface material, but it is typically used in conjunction with a chemically inert maskant to create patterns and/or designs on the workpiece; material removal amounts are typically small, and significant portions of the workpiece will not see any material removal. Neither CM nor CE is inherently focused on reducing a component’s surface roughness; both processes can have this effect, but this reduction/alteration of surface roughness is a byproduct rather than a primary deliverable in most cases.
Chemical polishing (CP), much like CE, could be considered a derivative process from CM, but where CM focuses on bulk surface material removal, CP focuses on the efficient alteration of surface texture. This efficient alteration of texture is typically embodied by seeking to minimize material removal while maximizing roughness/texture reduction.
All three processes use an “active” chemical solution capable of spontaneously dissolving metal from the surface of the part(s). These active chemical solutions are typically a mixture of strong acids or bases. Some of the novelty and differentiation of the three processes can come down to the differences in these chemical solutions. CM being focused on bulk material removal requires chemical solutions that are fairly easy to maintain in order to ensure cost efficiency. CE and CP, which typically require lower levels of material removal, can focus more on process control.
Perhaps the most notable strength/advantage of purely chemical processes is their ability to remove material with a high degree of uniformity from geometrically complex components. Given that the only requirement for process efficacy (assuming a well-developed chemical formulation/process is being used) is the ability for the chemical solution to contact the surface of the part, chemical processes offer high levels of flexibility regarding part shape. Additionally, chemical processes will not induce any mechanical or residual stresses into the component(s), and they may be able to increase corrosion and/or fatigue resistance depending on the nature of the part and its prior forming steps.
Potential weaknesses/disadvantages of purely chemical processes are, most notably, the complications/requirements associated with the handling of generally harsh chemicals. In most cases, processing fumes will be generated that must be extracted and/or scrubbed before they are exhausted into the environment. Liquid waste will be generated from the process that often will need to be neutralized prior to industrial disposal. Protective equipment must be worn by operators who work closely with or around the chemical solution, especially for formulations designed for more chemically inert materials such as superalloys and refractory alloys. Lastly, if the process and/or chemical formulation is not well developed or is improperly applied, there is a risk of chemical attack to the part(s).
As with all tools, purely chemical processes have their place in the overall manufacturing supply chain. Despite some of the above-referenced challenges that are inherent to these processes, their value can outweigh their weaknesses for the right applications or use cases (see Figures 1 and 2). While CM, CE, and CP may not be thought of as common processes in the gear manufacturing industry, nital etch inspection is (or at least could be) considered a form of CM or CP. While the purpose of nital etch inspection is not to remove bulk material or to controllably alter surface texture, it is a strong acid-based chemical dissolution process and thus would meet the general criteria to fall under the definition of one or both of these processes.
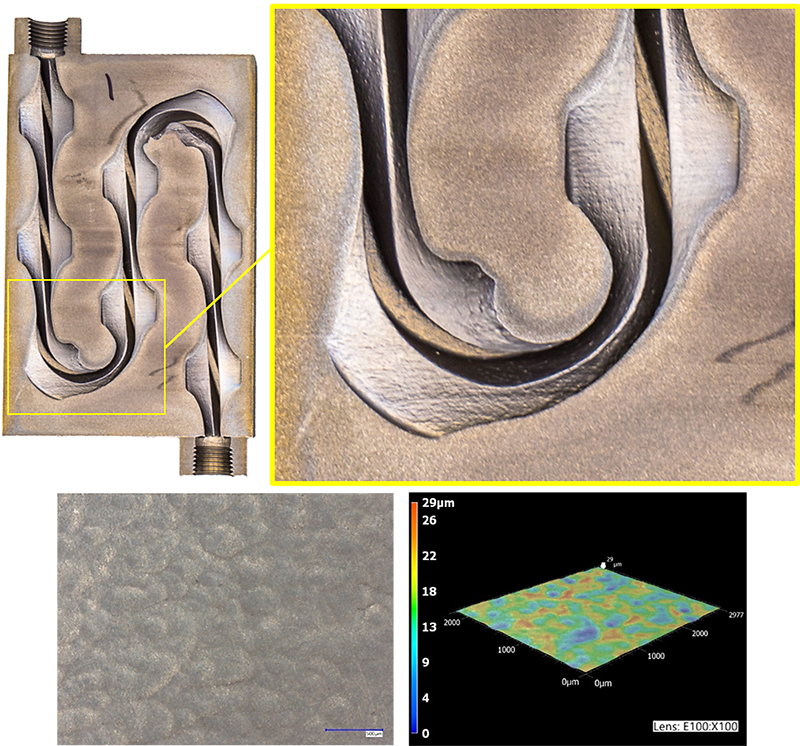
Figure 2: Example of internal surfaces after the application of an effective chemical polishing process.
Non-spontaneous electrochemical processes
Similar to purely chemical processes, there are several types/variations of subtractive electrolytic/electrochemical processes which have strong high-level similarities as well as important differences. The two primary subtractive electrochemical processes are electrochemical machining (ECM) and electropolishing (EP). Both processes rely upon a forced electrochemical reaction to dissolve/remove metal from a component. The reaction occurs by submerging the workpiece (which will serve as the anode) and a cathode in an electrolyte and applying a current or potential to induce metal dissolution from the workpiece. Both processes can use controlled or fluctuating (sometimes called pulsed) current/potential.
Similar to CM, ECM is a “bulk material removal process.” However, ECM is, in many ways, more comparable to CNC milling than it is to CM as ECM is primarily a forming process (which can also achieve surface finishing). Conversely, EP is more comparable to CP in that its primary purpose is to improve surface roughness/texture. However, EP would generally be more comparable to CM (as opposed to CP) due to its use of a largely generic cathode to drive processing cost efficiency. ECM requires a custom or purpose-built cathode which must be the reciprocal of the to-be-generated part geometry. In this dynamic, ECM may be more closely compared to CE; however, CE is not generally used as a primary forming process. The reason for the differences between the two cathode types (generic vs. purpose-built) is due to the nature of electrochemical processes.
Material removal rates in electrochemical processes are driven by current density which, in turn, is primarily driven by the distance between the anode and cathode as well as the “accessibility” or “biases” of the workpiece surface to current/potential differential (see Figure 3). Thus, EP will tend to have material removal variations from different surfaces of at least moderately complex geometries due to variations in current density. Because EP is most commonly used for lower levels of material removal, these material removal variations may not be problematic for many applications. ECM, by using a custom cathode designed to be the reciprocal of the final part geometry, is able to maintain a much more even current density during processing provided that the cathode is able to be moved during the process to maintain the cathode to anode distance.
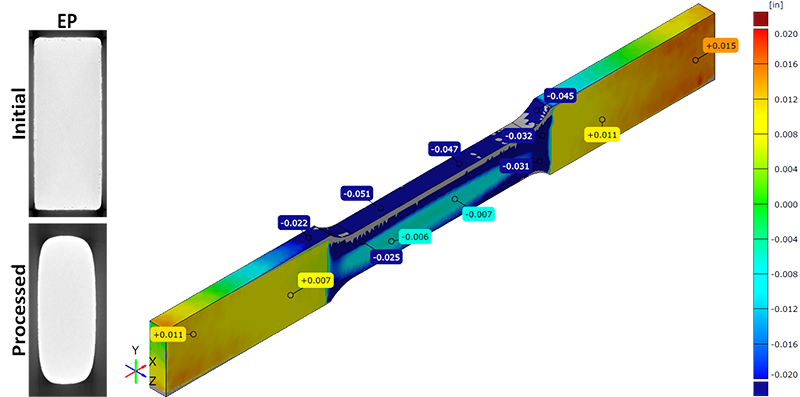
Figure 3: X-ray CT scan examples of shape alteration caused by EP (left) and blue light 3D scan showing surface material removal variances on a specimen processed by EP (right).
A primary advantage of electrochemical processes is their ability to produce “good” surface finishes in reactive materials in a short period of time. Some of these reactive materials include highly chemically resistant metals such as cobalt and nickel superalloys. Compared to CM, EP or ECM would generally produce a better final surface finish; even CP will tend to fall short of EP/ECM relative to the final roughness value obtained for these alloys. Further, both CM and CP will generally use more hazardous chemicals than what is used in the EP/ECM electrolyte (although it should be noted that many electrolytes will still contain strong acids and other hazardous chemicals). Thus, for applicable materials, these electrochemical processes will produce smoother final surfaces. However, material reactivity varies by alloy and there are alloys where EP/ECM have limitations relative to material removal efficacy and/or the final surface quality (ex. titanium).
The primary disadvantage of electrochemical processes is linked to their dependence on current density. As noted above, current density variations will drive dissimilar material removal and undesirable shape alteration without a custom cathode. Additionally, because of the nature of electrochemical processes, in that they only target surface asperity “peaks,” they have limited benefit in improving mechanical fatigue resistance. While the environmental, health, and safety considerations for electrochemical processes are reduced as compared to purely chemical processes, many electrolyte solutions are still fairly hazardous. Research is actively being conducted to reduce the hazardous nature of these electrolytes and some “dry” EP processes have emerged that reduce operator risks. Specifically in reference to “dry” EP processes, the advantages of removing the acidic, liquid-based electrolyte are at least somewhat offset in reductions to process efficacy linked to processing time and material removal capacity; additionally, the dry electrolyte must still be dealt with from a waste management perspective. Lastly, there is a risk of pitting if the process is improperly applied/controlled.
As with pure chemical processes, electrochemical processes have their weaknesses, but they also have some strong use cases. ECM can be a strong alternative forming operation to CNC milling and casting for moderately complex geometries. EP can be a strong final polishing step for parts that have substantial volume and can accommodate either the setup costs of a semi-custom cathode or the material removal variances of a generic cathode. Neither process is overly prevalent in the gear manufacturing industry, but both could certainly be used if the need arose.
In conclusion, subtractive electrochemical and purely chemical processes have a fundamental difference in their material removal mechanism which creates differing strengths and weaknesses. Within both of these categories of processes, there is a subset of relatively similar yet unique processes that exist. Understanding the differences between these subset processes is important in the selection of the appropriate material removal/surface finishing solution for your application.
References
- Diaz, J. Michaud, T. Mikulas, J. Boykin, N. Shamsaei, S. Shao, S. Lee, J. Pegues, T. Hall, J. Stull, T. Duffy, A. Mirabal, P. Gradl, 2024. “Surface post-treatment of additively manufactured components.” Additive Manufacturing of High-Performance Metallic Materials, R. Pederson, J. Andersson, S. Joshi (Eds), pgs. 223 – 284, Elsevier (https://doi.org/10.1016/B978-0-323-91885-5.00008-1)
- D. Landolt, Fundamental aspects of electropolishing, Electrochim. Acta (1987) 32, (https://doi.org/10.1016/0013-4686(87)87001-9)
- K. Arvind, S. Apporva, K.S. Ashwin, H. Sumanth, T. Nanjundeswaraswamy, Chemical blanking and chemical milling process: an outline, J. Eng. Res. Appl. 9 (2019) 83–86, (https://doi.org/10.9790/9622)
- M.M. Basha, S.M. Basha, V.K. Jain, M.R. Sankar, State of the art on chemical and electrochemical based finishing processes for additive manufactured features, Addit. Manuf. 58 (2022), 103028, (https://doi.org/10.1016/j.addma.2022.103028)
- P.A. Jacquet, On the anodic behavior of copper in aqueous solutions of orthophosphoricacid, Trans. Electrochem. Soc. (1936) 69, (https://doi.org/10.1149/1.3498234)
- G.A. Longhitano, M.A. Larosa, A.L.J. Munhoz, C.A. de Carvalho Zavaglia, I. MCF, G.-
- A. Longhitanoa, et al., Surface finishes for Ti-6Al-4V alloy produced by direct metal laser sintering, Mater. Res. 18 (2015) 838–842, (https://doi.org/10.1590/1516-1439.014415)
- www.voxelinnovations.com
Article reposted with permission from: https://gearsolutions.com/departments/materials-matter/subtractive-chemical-processes-differentiated-and-explained/
By Justin Michaud
March 15, 2025
Numerous chemical processes exist for the removal of metal. These processes are commonly referred to incorrectly and/or conflated with one another. This column seeks to differentiate some of these processes while also providing some commentary on their strengths and weaknesses.
Download Resource
Please fill out the information below to receive the selected resource.
Download Resource New Form
Please fill out the information below to receive the selected resource.