
INTRODUCTION
Laboratory and field testing of specimens and gears superfinished with chemically accelerated vibratory finishing incorporating high density non-abrasive ceramic media has been shown to greatly extend cycle life due to reductions in pitting and wear [2]. The isotropic surface generated is unique when compared to even the finest honing and lapping in that it has no directionality and a final Ra < 0.08 μm. The texture consists of only random scratches and shallow dents. The current interest was to determine if this finish would also benefit scuffing resistance. In addition, specimens were superfinished with this process to an even smoother surface (Ra < 0.02 μm) to determine if it imparts still better performance. The much smoother surface was generated using non-abrasive plastic media instead of ceramic. Both superfinished surfaces were tested for scuffing resistance and compared to specimens with varying surface roughness.
DESCRIPTION OF THE TEST
Testing Apparatus
The scuffing test bench as described by Patching et al. has been developed entirely at Cardiff University and is fully described elsewhere [1]. Apart from the high speed/high temperature capability other special features are the use of crowned discs to give a self-aligning contact, and axial finish of the disc surfaces, which reproduces the orientation of finish found on most types of gears. The machine was designed to impose a maximum load of 4 kN at the contact which, for the geometry chosen (i.e., 76.2 mm diameter discs, nominally 10 mm wide, each with 304.8 mm crown radius) gives a maximum Hertzian contact pressure of about 1.7 GPa. The bulk temperature at the surfaces in the inlet to the lubricated contact that is of key importance in elastohydrodynamic lubrication is measured by embedding thermocouples just beneath the surface of both discs. The tangential friction force between the discs is measured by monitoring the torque in the shaft driving (or, strictly braking) the slower speed test shaft.
The load applied to the contact between the discs is carefully controlled. The load is increased at intervals of three minutes until either scuffing failure is detected or the load limit of the machine is reached before a scuff occurs. The increment by which the load is increased at each stage was chosen to give a constant increase in the dry contact (Hertzian) pressure for a nominally smooth surface. The load stages and the corresponding loads and maximum Hertzian pressures are given in Table 1.
To conduct a test the machine is assembled with the discs and shafts in place. The test oil is first heated to the desired oil feed temperature. During this period the test oil is circulated through the test head so that static thermal equilibrium of the machine is attained. The test oil is heated to 100 oC and the gearbox oil to 45 oC. A light load is then applied through the hydraulic ram to bring the discs into light static contact (typically 100 N).
The disc temperatures and friction forces are continually recorded. The main drive motor for the machine is then started and the speed gradually increased manually up to the pre- determined speed for the test. The machine is allowed to run for typically three minutes, to allow the bulk temperature of the two discs to stabilize. Then the first load of the standard loading sequence is applied.
As the test approaches the load at which a scuff is expected, a careful watch is made for scuffing. Scuffing produces an unmistakably sharp rise in friction accompanied by corresponding rapid increases in the temperature of both discs. The load is released and the machine is turned off and allowed to cool. The discs are then inspected to confirm scuffing.
Description of the Disc Specimens
Ground case carburized disc test samples were supplied by Cardiff University to REM Chemicals, Inc. The base material was AMS 9310 and heat treatment was performed to aerospace type specification as listed in Table 2. Each disc had a diameter of 76.2 mm and a diameter of approximately 10 mm with a 304.8 mm crown radius. At the machine’s maximum load of 4 kN, a maximum Hertzian contact pressure of about 1.7 GPa is attained. The test samples used were axially ground at Cardiff University, rather than in the more usual circumferential direction. An axial finish simulates the orientation of roughness in gears where rolling and relative sliding of the surfaces occur in a direction perpendicular to that in which the surfaces are finished. The typical level of surface roughness for the as-ground discs is Ra = 0.4 μm.
DESCRIPTION OF THE SUPERFINISHING PROCESS
Chemically Accelerated Vibratory Finishing
Details of superfinishing using chemically accelerated vibratory finishing have been published in detail elsewhere [2, 3]. The following is a brief summary of the technique. The superfinishing is produced in vibratory finishing bowls or tubs. An active chemistry is used in the vibratory machine in conjunction with media. When introduced into the machine, this active chemistry produces a stable, soft conversion coating on the surface of the metal part(s) being processed. The rubbing motion across the part(s) developed by the machine and media effectively wipes the conversion coating off the “peaks” of the part’s surfaces, but leaves the “valleys” untouched. (No finishing occurs where media is unable to contact or rub.) The conversion coating is continually re-formed and rubbed off during this stage producing a surface smoothing mechanism. This process is continued in the vibratory machine until the surfaces of the part(s) are free of asperities. At this point, the active chemistry is rinsed from the machine with a neutral soap. The conversion coating is rubbed off the part(s) one final time to produce the superfinished surface. In this final step, commonly referred to as burnishing, no metal is removed.
Media Description
Two different medias were used to determine the effect of surface roughness on scuffing resistance. Three sets of discs were superfinished using a high density non-abrasive ceramic media yielding a final roughness level of about 0.033 μm (Ra). Two other sets of discs were superfinished using a light non- abrasive plastic media and had a final roughness level of about 0.017 μm (Ra). The physical properties of the two media are shown in Table 3 and images are shown in Fig. 1.
SEM images of the surfaces of the two medias are shown in Fig. 2. Notice that the FM-9 has protuberances, which can cause light scratches on the surface. On the other hand, the plastic media has plateaus of non-abrasive calcined alumina, which will give a more polished effect.
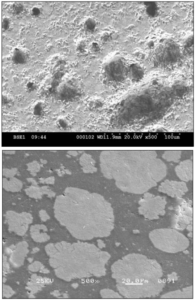
Fig 2. SEM images at 500X of the ceramic (top) and plastic (bottom) media used to superfinish the surface of the specimens.
Superfinished Surface Characterization
The superfinished surfaces produced by the two media are radically different. See Fig 3. It is apparent that the superfinished surface produced with the non-abrasive high density ceramic media has a more textured appearance, whereas the lighter non-abrasive plastic superfinished surface is much smoother.
Three surface traces were taken approximately 120o apart on four discs finished with the non-abrasive ceramic media and four discs with the non-abrasive plastic media by Cardiff University. Fig. 4 is an example of the surface trace of a disc superfinished with the ceramic media, and Fig. 5 is an example of the surface trace of a disc superfinished with the plastic media.
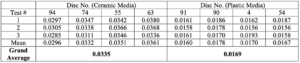
Table 4. Surface roughness measurements (microns) taken approximately 120o apart on four discs finished with the non-abrasive ceramic media and four discs with the non-abrasive plastic media.
It can be seen that the discs superfinished with ceramic media had a surface roughness of approximately twice that of the discs finished with the plastic media.
The crown on the specimens was also measured after the superfinishing step. The crown was the same before and after superfinishing for both the ceramic and plastic superfinished discs. No change was expected since the superfinishing removes only approximately 0.0025 mm of stock.
BASELINE SPECIMENS
Zinc Chip Superfinished Discs
In previous papers by Patching et al. [1,4], specimens were superfinished by a proprietary superfinishing method in which the as-ground discs are immersed in a vibrating bath containing water, abrasive powder and small zinc chips. The discs take on an almost mirror finish and an Ra of < 0.1 μm can be achieved. These superfinished discs were tested under identical conditions to the discs superfinished using chemically accelerated vibratory finishing, and therefore the effect of these different superfinishing processes on scuffing can be examined.
As-Ground Discs
In a previous paper, Patching et al. [1] also tested as- ground specimens. These were identical to the ones described earlier.
RESULTS
CONCLUSIONS
- The chemically accelerated vibratory finished discs using ceramic media experienced no scuffing even after extending the test time to 30 minutes at the highest test load. This preliminary data shows it has surface characteristics that help resist scuffing under the test conditions.
- The much smoother chemically accelerated vibratory finished discs using plastic media, scuffed at an unexpected much lower load.
- It may be postulated that the surface texturing from the ceramic media aids in the lubrication process. A smoother surface is not necessarily better. More testing needs to be done to establish this.
- The zinc chip superfinished discs outperformed the plastic superfinished discs, but did not give the remarkable performance of the ceramic superfinished discs.
REFERENCES
Download Resource
Please fill out the information below to receive the selected resource.
Download Resource New Form
Please fill out the information below to receive the selected resource.